by
[user not found]
| Jul 27, 2015
If you've seen concrete before, it was likely used for a sidewalk, a road, someones patio or maybe even a house.
But in recent years concrete technology has become more advanced and the applications of concrete are becoming more and more diverse. Concrete is finding it's place in new and exciting applications and places.
Some companies around the world are exploring how to build concrete walls and forms that don't disrupt the environment. Others are figuring out ways to illuminate concrete, taking decorative concrete to a whole new level. And some are even making coffee machines, chairs and other furniture out of concrete and seeing fantastic results.
In this post, we're going to explore some of the new concrete developments and applications that companies around the world are making happen.
1. GrassConcrete's Environmentally Friendly Concrete Forms
"Our belief lies in establishing better and more sustainable ways to build, where development need sits in harmony with our natural world."
That quote comes from Bob Howden, the Managing Director of a concrete company in Yorkshire, the United Kingdom called GrassConcrete Limited.
GrassConcrete Limited produces a number of environmentally-friendly concrete products for roads, roofs and walls including a product called GrassCrete. GrassCrete is a reinforced cellular concrete wherein grass can be grown from it's cavities.
GrassCrete has been used mostly in urban settings. The lasting strength of concrete allows cars and vehicles to drive over it while the added greenery helps to break up the browns, greys and blacks of the city.
As explained in this video from GrassConcrete Limited every new GrassCrete installation process begins with removing the top soil layer from the worksite.
Next, a sandline is put down replacing the top soil. Plastic star shaped forms are then laid down on top of the sand line. Once the top soil and seed are spread, grass will grow from these plastic forms.
Next, rebar spacers are laid down in between the grid pattern of the plastic forms. Flowing concrete is laid down on top of the entire form and squeegeed around for an even surface. Once the concrete has hardened, the star-shapes are dug out and a layer of top soil is spread out on top followed by grass seeds.
According to the above video, GrassCrete can be applied in many different areas and showcase many different benefits including:
- helping to improve natural water runoff and drainage
- providing a better surface for heavy vehicles or emergency vehicles to park on during an emergency event
- improving slope protection efforts
GrassCrete can also:
- endure loads up to "40 tons gross vehicle weight"
- reduce sub-base depths and
- resist differential settlement damage and changes
and can be applied to:
- embankment and spill protection efforts
- flood alleviation projects
- reservoir lining construction
GrassConcrete has used their technology all over the world. In one instance in Powys, UK, there was a problem with flooding. Grasscrete was used on the shoulders of the highway to help with drainage and maintaining run-off.
In areas where an overt area of pavement may not be preferred, Grasscrete offers the perfect, low profile solution. While using concrete to maintain structure isn’t a new concept, the reworking of it’s traditional application is what makes this company’s products so useful.
*The above images are from of GrassConcrete's website.
2. Translucent Concrete with LUCEM, LiCrete and More
When you think of concrete, the first thing that comes to mind is most likely not “light transmitting.” Chances are, light transmitting wouldn’t be a thought that would enter your mind at all when thinking about concrete. However, LUCEM LICHTBETON, a German company alongside Florack Bauunternehmung, LBM EFO, Luccon Lichtbeton and LiCrete has been on the forefront of translucent concrete technology, making impressive strides in this technology and carving out it's applications and uses.
Translucent concrete, also known as light transmitting concrete, added a colorful, mesmerizing new dimension to the typical grey, opaque building material. RWTH Aachen University, is one of the most noteworthy cases of using this luminescent concrete:
When the concrete is not illuminated, it remains opaque like ordinary concrete. But when the lights in the building are turned on the building exterior lights up with a brilliant spectrum of colors transforming the building from gray to a colorful work of art.
Translucent concrete works by using fiber optic cables embedded in concrete. According to one article:
"Translucent concrete isn't exactly "see-through," but the new building material draws on optical fibers to transmit light through it while retaining the density that has literally made concrete the cornerstone of buildings around the world."
The article goes on to elaborate exactly how the optical fibers creates the translucent effect:
"The fiber strands, which attract and transmit both natural and artificial light, make up about 5 percent of a translucent concrete block's surface volume. The fibers are mixed with traditional concrete components -- water, sand and cement -- and are distributed evenly throughout the surface. Through the resulting translucent panels, a viewer can clearly see the outline of an object on the opposite side of the concrete. Despite this clarity, however, translucent concrete retains its stout, crack resistant, load-bearing quality.
The light transmitting material is largely believed to have been invented by Hungarian architect Aron Losonczi, who began developing pre-fabricated translucent concrete blocks he called LiTraCon (light transmitting concrete) in 2004, just three years after graduating from Budapest's Technical University. Here, the manufacturer hand-molds large pieces of concrete, embedding thousands of strands of optic fiber in the material at the same time. The concrete is then cut into individual blocks (the smallest are about 48 x 14 inches, or 1.22 x .35 meters). The parallel fiber strands create two distinct grain-type surfaces: one bright and the other dark."
3. Floating Concrete Docks with Bradford Marine
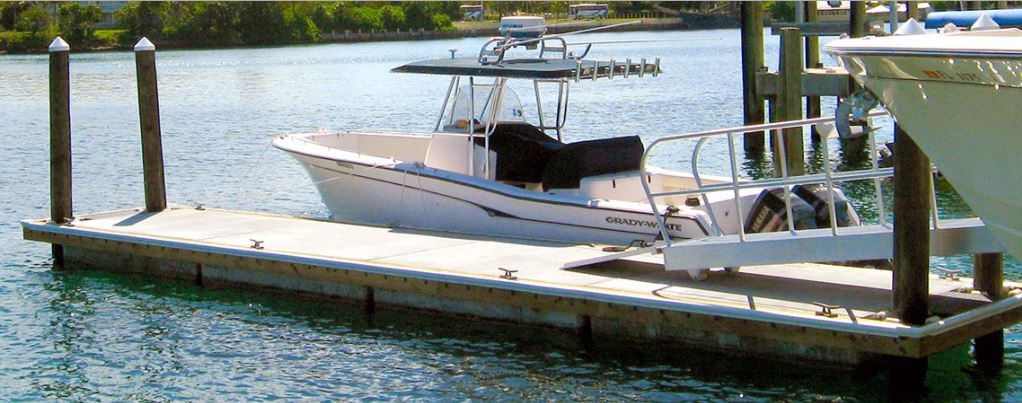
Concrete is not the most buoyant material, but with a little bit of additional engineering concrete can hold itself above water.
Floating concrete docks provide a durable, lasting solution to marina owners and yacht users. Concrete takes a very long time to degrade in water, removing any possibility of a dock needing to get replaced as a result of rot or wear.
As one manufacturer of floating concrete docks, Bradford Marine explains with regard to the manufacturing process:
"Floating concrete dock flotation units consist of a fiber-reinforced concrete shell with a polystyrene foam core. Concrete is reinforced with galvanized steel wire mesh with use of galvanized reinforcing steel as an additional manufactured design. Reinforcing bars are provided at corners and along edges of the concrete shell."
While the concrete itself is nothing out of the ordinary, Bradford Marine has designed a way to make the material more durable and sufficiently buoyant to be used in docking.
Wrap Up
These few applications are testimony to the realm of possibilities available when retooling old technology. While concrete is still a building material as it was intended to be, its usages have expanded significantly. The modifications mentioned above have given light to new subsets of the concrete industry--subsets that most likely wouldn’t have come into existence without someone asking questions allowing them to explore new options.
As you go about your day, challenge yourself to question each interaction you have, whether it be with a piece of technology or a person, and think about ways that these ordinary interactions could be rekindled into extraordinary ones. You may think of a way to change something that would not only benefit you, but those around you!